Cybersecurity Strategies and Best Practices for Manufacturing
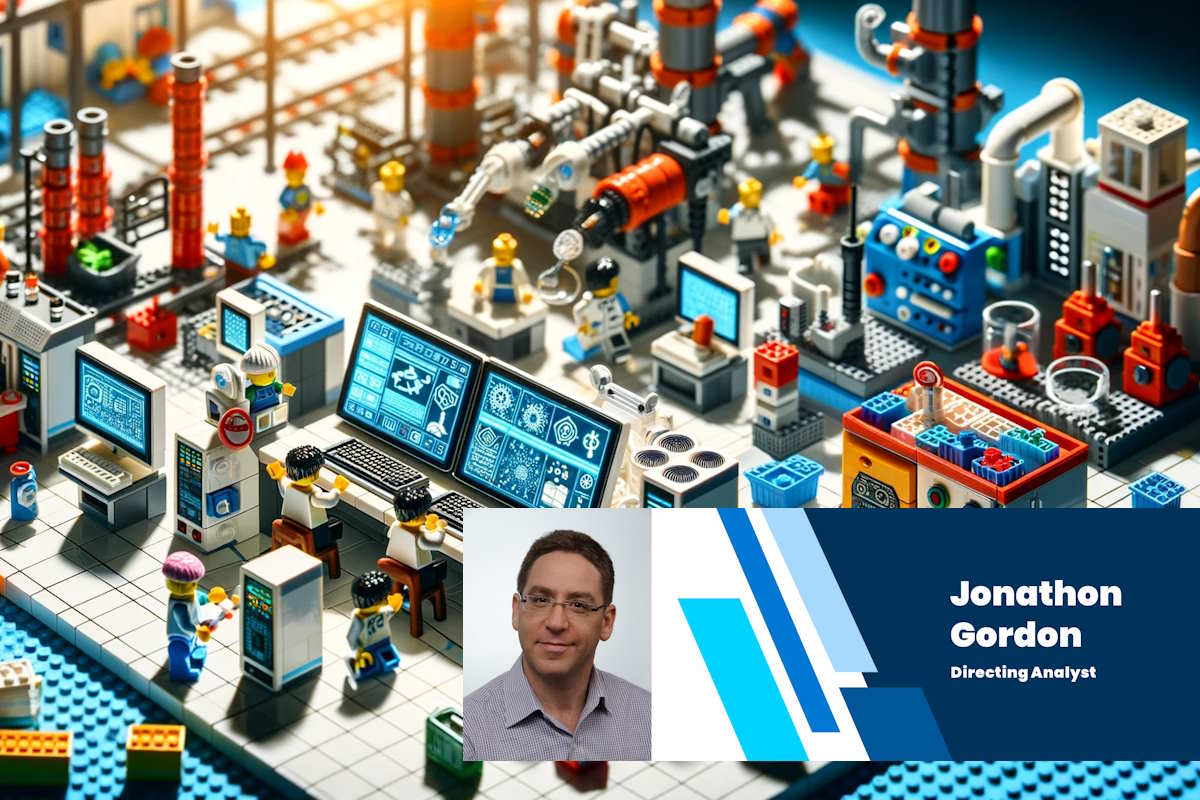
Hello there, and a very Happy New Year 2024 to all of you! Welcome back to our article series where we’re diving deep into the world of industrial cybersecurity, specifically in the manufacturing sector. As we step into this new year, it’s more important than ever to stay ahead in the cybersecurity game. Today, we’re tackling Cybersecurity Strategies and Best Practices in Manufacturing. While we won’t be able to cover every nuance, we aim to provide valuable insights and provoke some thought-provoking ideas. So, grab a cup of coffee (or two), and let’s get into it with fresh perspectives for this exciting new year!
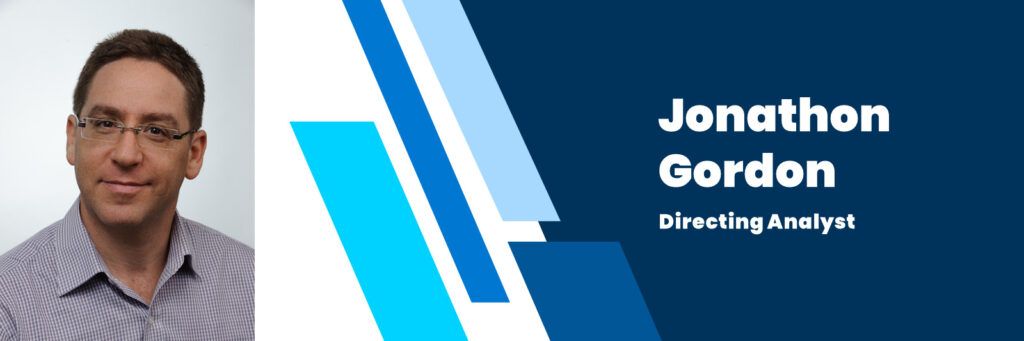
The Crucial Need for Securing Manufacturing Operations
In today’s digital age, securing manufacturing operations has become more crucial than ever. With increased connectivity, evolving cyber threats, regulatory requirements, and the ever-present need for business continuity, it’s clear that comprehensive cybersecurity strategies are vital. This means getting everyone on board, from stakeholders to the teams on the ground, and implementing policies that follow a defense-in-depth approach.

Emphasizing Cross-Functional Collaboration: OT, IT, and CISO Teams
A pivotal element of our cybersecurity strategy is the fostering of robust collaboration between Operational Technology (OT), Information Technology (IT), and Chief Information Security Officer (CISO) teams. This cross-functional teamwork is not just beneficial but essential in today’s interconnected industrial landscape.
Each group contributes a distinct and invaluable skill set. OT teams have an in-depth understanding of assets and processes, IT teams excel in constructing and managing secure network infrastructures, and CISO teams are the vanguard in identifying and mitigating cyber threats. The outdated notion of OT and IT/CISO operating as separate silos is not just obsolete; it’s a hazardous mindset. In the absence of trust and collaborative synergy, industrial organizations expose themselves to heightened risks.
From the outset of a project, especially during the proof-of-concept phase, it’s imperative to prioritize this cross-functional collaboration. This collaborative approach is instrumental in selecting the most suitable tools and technologies, and it plays a critical role in reducing resistance during the deployment phase. The project team should spearhead this collaborative effort, skillfully navigating through challenges and ensuring that every step aligns with the primary objectives of OT cyber monitoring and risk mitigation. This integrated approach not only enhances the effectiveness of cybersecurity measures but also fosters a culture of shared responsibility and proactive defense against emerging cyber threats.
The Foundation of Manufacturing Cybersecurity: Starting with Asset Visibility
In the realm of manufacturing cybersecurity, the importance of asset visibility cannot be overstated. This critical process involves developing a comprehensive registry of all OT/ICS devices, detailing each device’s specifications, software versions, network roles, and operational data. Far from being a mere procedural step, this registry forms the backbone of effective risk management and ensures the reliability of operations in industrial settings. By enabling organizations to identify potential vulnerabilities and threats, these detailed inventories play a pivotal role in the secure and efficient operation of ICS/OT environments. They go beyond merely keeping operations running smoothly; they are integral in managing cybersecurity risks and vulnerabilities, and preparing for incident responses. The creation and maintenance of these inventories require careful planning, a combination of physical checks and network-based techniques, and strong security measures to protect the sensitive information they contain.
A crucial aspect of navigating these challenges is the recognition that OT assets themselves can be potential sources of vulnerabilities. To mitigate these risks, simple yet effective measures can be implemented. Disabling unused ports on devices and ensuring secure physical access to critical equipment are foundational steps that can significantly bolster the security of these systems.
Moreover, adhering to established standards is vital. Compliance with frameworks like ISA/IEC 62443-4 is not just about following best practices; it’s about creating a secure and resilient operational environment from the ground up. This also extends to the selection of products and solutions. Choosing equipment and software that have been designed with security considerations at every stage of their lifecycle is essential. This approach ensures that security is not an afterthought but a fundamental aspect of the entire system.

Evolving Cybersecurity Strategies in Digitized Manufacturing
In traditional manufacturing operations, the primary defense against cyber threats involved establishing strong perimeter defenses, such as deploying firewalls. However, as factories increasingly digitize and the need for seamless integration with enterprise IT and cloud resources grows, the once-effective airgap approach is no longer sufficient. Today, there is a pressing need for highly granular security policies that are specifically tailored to protect each OT asset on the factory floor. This shift towards more refined and asset-specific security strategies is crucial in addressing the unique challenges posed by modern, interconnected industrial environments.
The Importance of Granular Visibility in a Defense-in-Depth Strategy
A crucial first step in any defense-in-depth strategy is achieving granular visibility into your operations. This involves understanding not only what assets are connected but also the nature of the traffic being exchanged between them. In the manufacturing sector, this task is particularly challenging due to the localized nature of most network traffic within individual production cells. To effectively capture this traffic, it’s often necessary to monitor network activity at nearly every access-level switch.
Why Implement Network-Based Security Monitoring?
Network monitoring in OT/ICS environments is essential, serving both as a technical necessity and a critical aspect of an organization’s overall security posture. As these systems increasingly intertwine with IT networks and the broader Internet, the potential for security incidents escalates. Here are some key reasons why network monitoring is indispensable:
- Real-Time Threat Detection: Monitoring facilitates the real-time detection of anomalies and potential threats, which is vital in OT/ICS environments where even minor disruptions can lead to significant operational and safety consequences. Quick identification of threats allows for immediate response, minimizing the impact of any security incident.
- Compliance and Regulatory Adherence: Many industry standards and regulations, such as the NIST Cybersecurity Framework, require monitoring for compliance. Non-compliance can lead to security vulnerabilities, legal issues, and damage to an organization’s reputation.
- Facilitating Proactive Security Measures: Regular monitoring aids in the timely identification of vulnerabilities and security gaps, enabling proactive measures such as patch management, network segmentation, and adjustments to access control lists (ACLs).
- Bridging the IT-OT Divide: Effective monitoring plays a crucial role in safely implementing IT-like security measures within OT environments. This is particularly important for organizations that are navigating the complexities of integrating these two distinct operational spheres, ensuring a cohesive and secure operational environment.

The Emerging Role of ZTNA in Securing Manufacturing
It seems like you can’t browse through tech news these days without stumbling upon discussions about Zero Trust Network Access (ZTNA). Despite the buzz, it’s clear that ZTNA has a significant role to play in the future of securing manufacturing environments.
Rethinking Secure Remote Access
When we talk about secure remote access, traditional methods come with their own set of challenges. Cellular gateways or uncontrolled software products often lead to shadow IT issues, where IT departments lose visibility and control over the software used by their employees. VPNs, while popular, are not without their drawbacks. They are typically always-on solutions that can be complex to manage, especially when it comes to configuring and maintaining firewall rules.
The Advantages of ZTNA Solutions
This is where ZTNA solutions come into the picture. Gaining momentum in the cybersecurity world, ZTNA solutions stand out because they verify users and only grant access to specific resources. This verification is based on identity and context policies, aligning with the principle of ‘never trust, always verify’. In a ZTNA architecture, the process of defining and enforcing access policies is centralized, which not only simplifies management but also significantly enhances security.
As the manufacturing sector continues to evolve and embrace digital transformation, the role of ZTNA in ensuring secure, efficient, and cost-effective remote access is becoming increasingly important. Its ability to adapt to complex industrial environments while maintaining strict security protocols positions ZTNA as a key player in the future of industrial cybersecurity.
Moving forward
So, there you have it – a quick, but comprehensive look at cybersecurity strategies and best practices in manufacturing. From collaboration between OT, IT, and CISO teams to the implementation of ZTNA solutions, it’s clear that a multi-faceted approach is necessary to protect against evolving cyber threats. Stay tuned for more insights in our next chapter, and remember, in the world of cybersecurity, staying informed is your first line of defense!
In case you missed the first installments:
Part 1: Industrial Cybersecurity Manufacturing Cybersecurity in the Manufacturing
Part 2: The Journey Beyond Industry 4.0 – Embracing Smart Manufacturing
Part 3: Navigating the Manufacturing Threat Landscape