Cyber Incident Management, Response, and Recovery in Manufacturing Environments
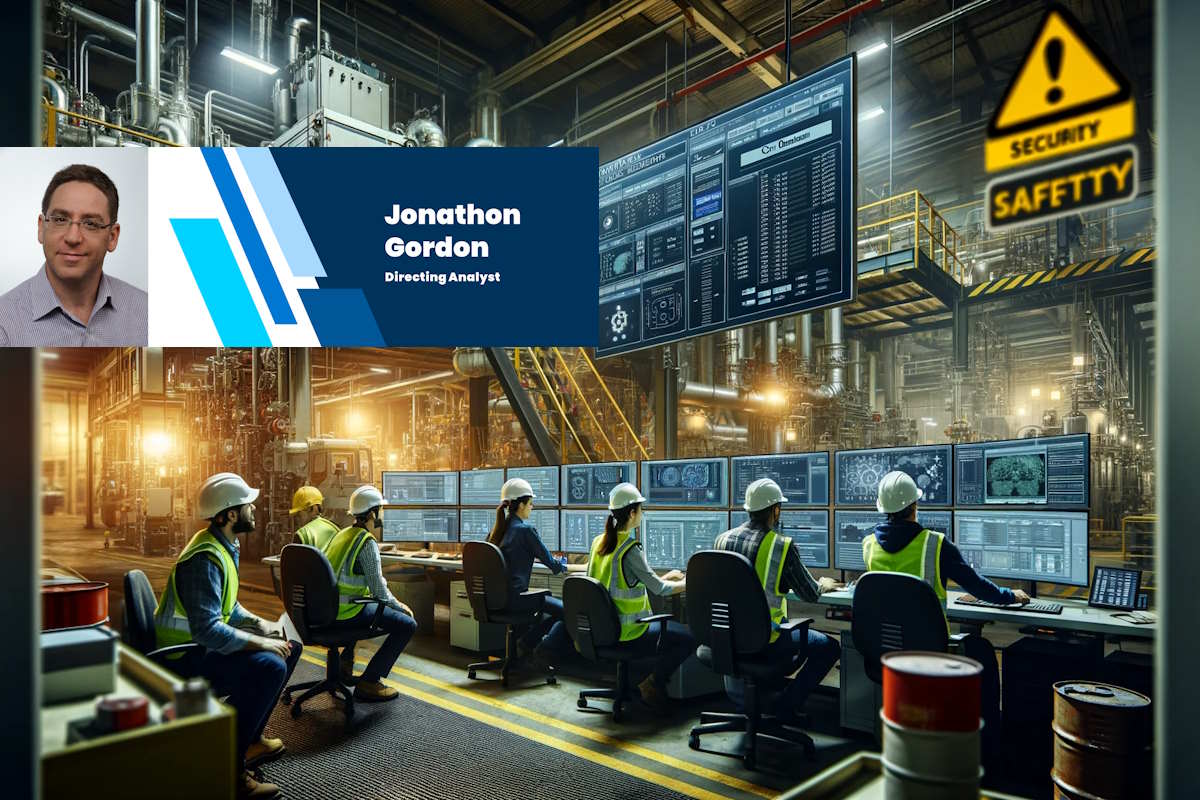
Hey everyone, welcome back to our latest chapter in the cybersecurity series for the manufacturing world. Let’s dive right into the thick of things. You know, despite all the cash pumped into cybersecurity defenses, the harsh truth is that cyber incidents are popping up more frequently than ever in industrial settings. And with regulations tightening the screws on accountability and transparency, it’s clear as day that having a rock-solid incident response plan is no longer optional – it’s critical for staying resilient in the face of cyber threats. But here’s the kicker – a lot of companies are still scrambling when it comes to rapid recovery and response.
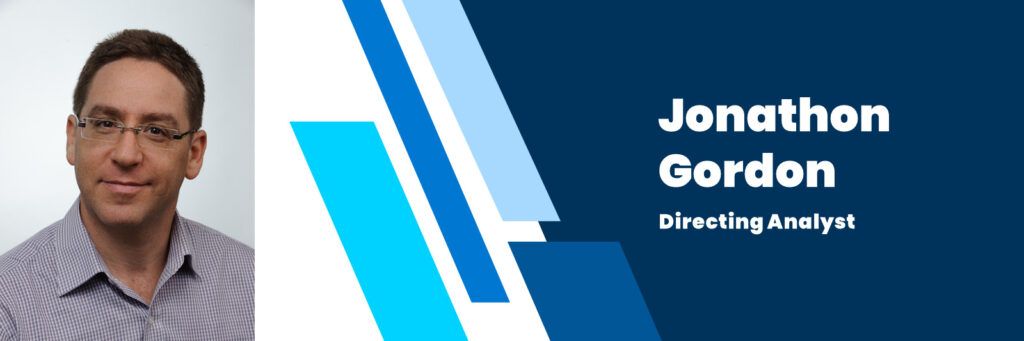
So, what’s the deal with organizations and their struggles? Well, research points to some core issues in handling incidents, especially due to a kind of ‘blind spot’ in their Operational Technology (OT) networks. The way forward? It’s all about tailoring an OT-specific incident response plan, packed with regular tests and expert insights.
In the world of manufacturing, where keeping things up and running safely and guarding sensitive data is paramount, facing up to these cyber threats head-on is crucial. Companies need to roll out detailed incident response plans. But it’s not just about reacting when things go south; it’s equally about staying a step ahead with regular vulnerability checks, training folks on cybersecurity best practices, and having a go-to incident response squad. And don’t forget – putting these plans through their paces with simulations is key to patching up any holes.

The Nitty-Gritty of Solid Incident Response Plans in Manufacturing Cybersecurity
Creating and putting an effective incident response plan into action is the bedrock of being cyber-ready. This kind of plan can seriously lessen the damage of cyber incidents, especially in places where OT systems are the lifeblood of physical machinery and infrastructure. We’re talking about not just protecting the bottom line here, but also keeping people safe. This means having a plan that’s slick and coordinated, covering various locations, processes, and systems – vital for keeping everything running smoothly and safely.
First things first, though. Having a top-priority incident response plan is your best bet to dodge operational downtime and tackle any safety or environmental red flags. The challenge for many teams is getting their heads around incident detection and escalation, often hamstrung by less-than-stellar monitoring capabilities and the cultural divide between OT and IT folks. That’s where clear guidelines and playbooks, made in advance, become game-changers. They’re like the secret sauce for effective communication and teamwork during crunch time, bridging the gap between different domains.
With cyber threats on the rise, the significance of a well-crafted incident response plan is skyrocketing. It’s all about organized and efficient handling of incidents, making sure everyone knows their part and what to do. This approach is a lifesaver in keeping operations running smoothly and safely, without any hitches.
When the Stakes are High: The Consequence-Based Approach in ICS Operations
Now, let’s talk about safety and reliability in Industrial Control System (ICS) operations – these are non-negotiable. Adopting a consequence-based approach is smart, especially since collecting forensic data can be a slow and steady affair. Keeping an eagle eye on ICS operations with continuous, effective network monitoring is crucial. Tuning your network monitoring just right to keep a close watch on ICS activities is the way to go. But here’s the catch – getting forensic evidence in ICS environments is often hands-on, manual work. Teams need to balance this against the potential downtime of critical systems. It’s a delicate dance between being thorough and keeping things moving.
Challenges pop up in detecting incidents, partly due to not-so-great monitoring, but also in figuring out when something’s serious enough to escalate. The different worlds of OT and IT teams often mean they’re not exactly speaking the same language. The fix? Well-crafted guidance and playbooks. These are like your roadmap for clear communication and decision-making, ensuring everyone can work together smoothly despite coming from different backgrounds.
Strengthening Incident Response in Manufacturing
Creating a strong incident response strategy is key for manufacturing organizations. We’re talking about a plan that covers all bases – detection, containment, eradication, and recovery. It’s about being ready for incidents, knowing how to spot and analyze them, having strategies to keep them in check, and procedures for collecting evidence and fixing issues. Plus, you’ve got to have clear reporting guidelines and recovery steps, along with ways to keep improving and learning. This kind of comprehensive approach makes sure no stone is left unturned in incident management, beefing up your defense against cyber threats.

But it’s not just about having a plan on paper. Everyone involved must know their role inside out. And you know what helps? Additional resources like playbooks lay it all out. Using the right tools and strategies within these frameworks is key to reducing the impact of cybersecurity incidents on your operations.
The real test of an incident response plan? How well your team knows it and can put it into action. That’s why running simulations and tabletop exercises is so important – they ensure your plan isn’t just theory, but something that works when the rubber meets the road.
A solid incident response plan isn’t just another document – it’s the foundation of a successful OT incident response function within your cybersecurity program. It’s about getting ahead of the game, identifying potential OT cyber incidents, and having strategies in place for quick detection, containment, and recovery. In the end, it plays a
crucial role in minimizing the fallout from cybersecurity incidents in manufacturing operations.
Teaming Up to Boost Manufacturing Cybersecurity
Now, let’s talk about teaming up for stronger cybersecurity. Manufacturing companies are increasingly joining forces with external stakeholders to beef up their cybersecurity game. This kind of collaboration is super valuable in managing and softening the blow from cybersecurity incidents within the sector.
When crafting an incident response plan, it’s vital to consider key external players like law enforcement and cybersecurity authorities, especially since there are legal bits and pieces to consider with cybersecurity incidents in manufacturing. It’s about knowing who to call and what to do when things go south. These external contacts can be a goldmine of extra support, insights, and guidance during an incident, really ramping up your response and recovery efforts.
Take Australia, for instance, where the Australian Cyber Security Centre (ACSC) is the go-to for cybersecurity incidents, offering help with containment, fixing issues, and connecting you to more government support. Over in the U.S., the cybersecurity scene got a major boost with the Cyber Incident Reporting for Critical Infrastructure Act of 2022 (CIRCIA), signed into law by President Joe Biden. This law, a big deal for national cybersecurity, sets strict reporting deadlines for cyber-attacks and pushes for modernizing government cybersecurity infrastructure. It’s all about making the country more cyber-resilient and ready to handle whatever comes its way.

In case you missed the previous installments:
- Part 1: Industrial Cybersecurity Manufacturing Cybersecurity in the Manufacturing
- Part 2: The Journey Beyond Industry 4.0 – Embracing Smart Manufacturing
- Part 3: Navigating the Manufacturing Threat Landscape
- Part 4: Cyber Risk in Manufacturing – A Closer Look
- Part 5: Cybersecurity Strategies and Best Practices for Manufacturing
- Part 6: Manufacturing Cybersecurity – Standards, Regulation and Compliance
- The Industrial Cybersecurity Handbook for Manufacturing